Tune
Basic composition of tuning windows and how to use them
The Tune windows in MotionLab3 are workspaces designed to allow manual tuning design and testing for the different modes of operation (current direct/quadrature, velocity, and position). These workspaces are formed by the following widgets:
Control (green box below) → widget use to modify the controller gains as well as additional parameters that can be useful during tuning operations.
Scope (orange box below) → widget use to plot the tuning response by comparing a signal generated from the drive and the response that the motor has for the specific loop (current, velocity or position).
Signal Generator (blue bow below) → widget use to generate the demand/reference signal that the user will try to tune the controller gains around. In an ideal case, the tuned signal should be exactly the same as this signal generated from the drive.
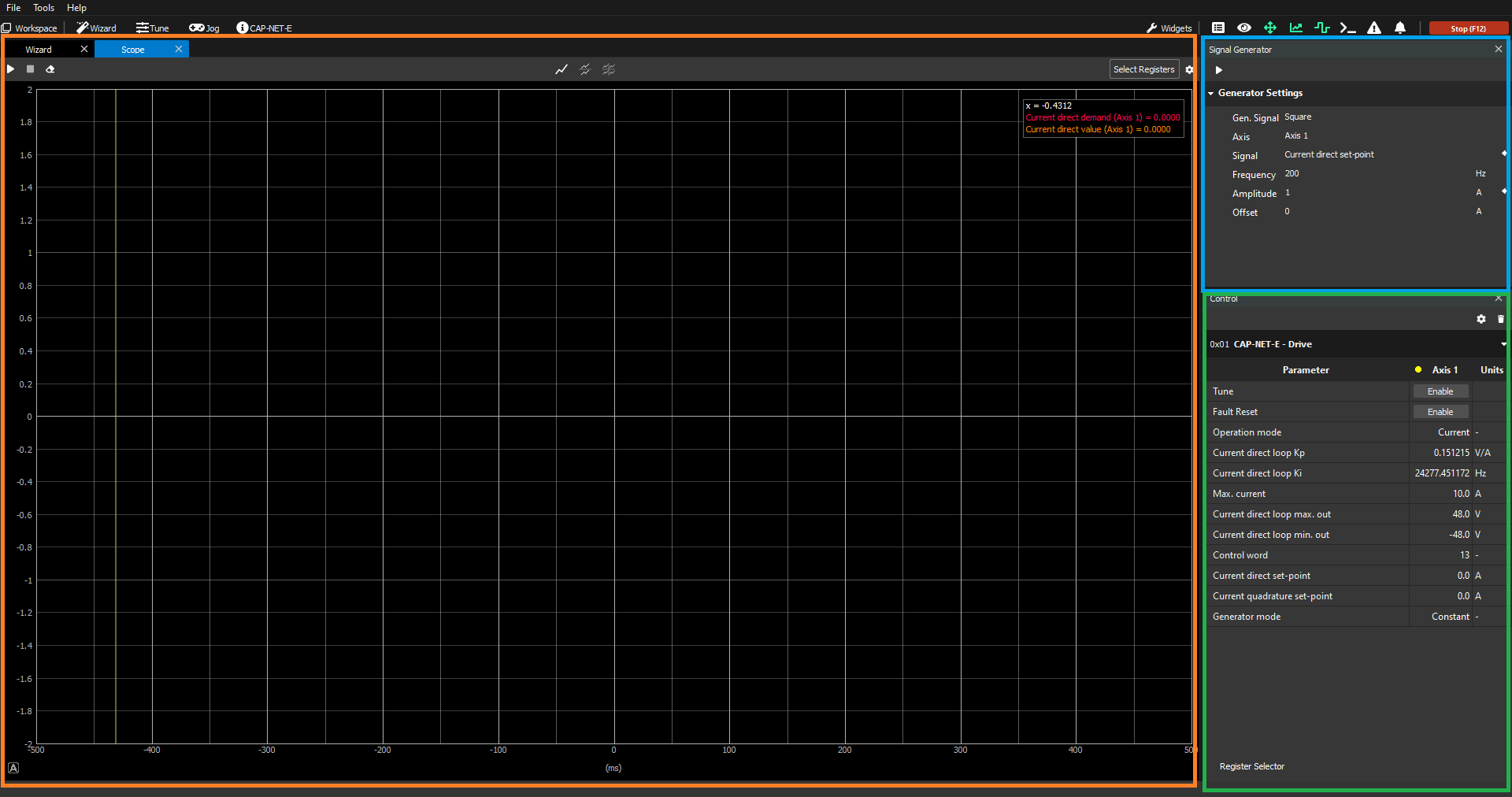
Once you click the "Enable Tune" button, you will start seeing in real-time the response of the system for the current gains of the PI/PID controller of the loop.
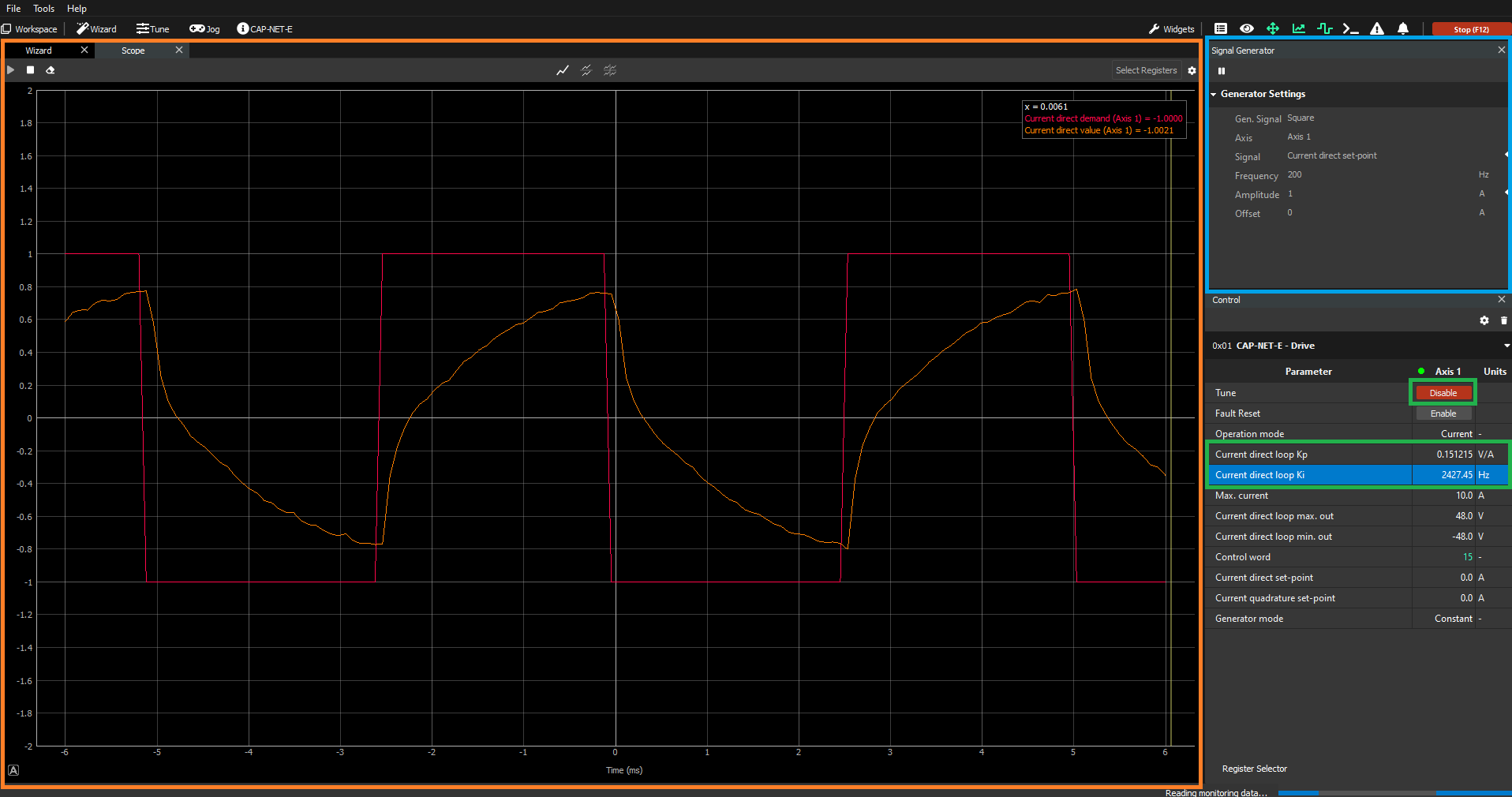
During this real-time representation of the response of the system, you can proceed to change the gains of the controller as you wish and see the updated response of the system for these new gains. This procedure is repeated until the performance of the PI/PID controller is acceptable and fulfills the needs of the user.
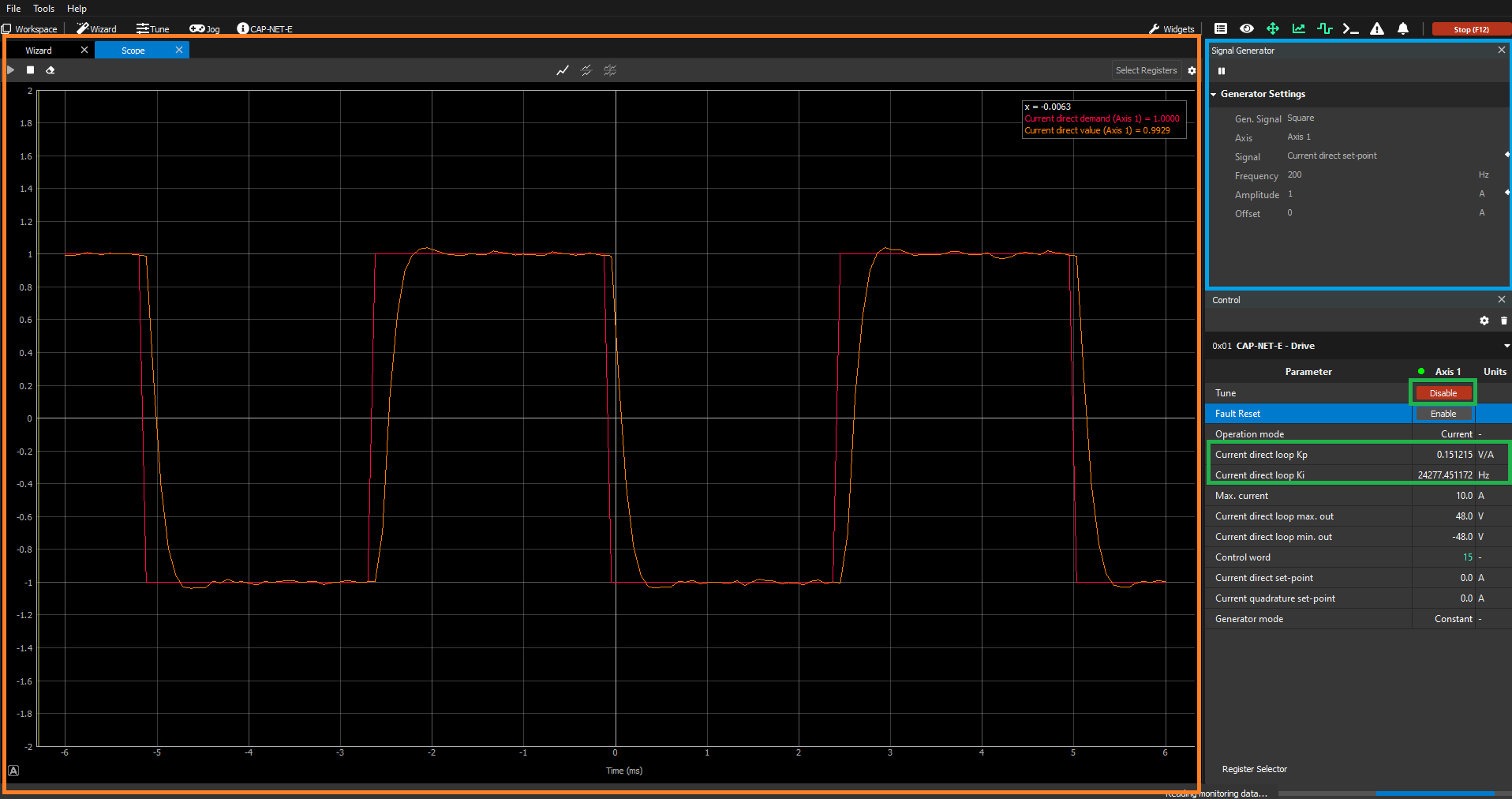
Current direct Tune window
If you want to get a deeper understanding of how this current direct loop is implemented inside the drive, please refer to the following documentation: Current modes (CSC, C, CA).
Parameters to tune
Kp → gain whose control action is proportional to the error between the current direct demand and actual values.
Ki → gain whose control action is proportional to the error between the current direct demand and actual values integrated over time.
Kr → gain that allows changing the controller architecture from an I+P (Kr = 0) controller to a PI (Kr = 1) controller. Intermediate values of Kr between 0 and 1 will provide a hybrid controller with both I+P and PI characteristics, weighted proportionally to the value of Kr.
Additional parameters
Current direct loop max. out → maximum voltage that will be applied to the phases of the motor. It acts as a saturator.
Current direct loop min. out → minimum (negative sign) voltage that will be applied to the phases of the motor. It acts as a saturator.
Max current → maximum current that will be applied to the phases of the motor.
Signal Generator
Gen. Signal → signal that with be generated with the settings below. For this workspace, this is the current direct set-point.
Signal → shape of the generated signal wave. At the moment this can only be a square wave.
Frequency → frequency of the generated signal in Hz.
Amplitude → amplitude of the demanded signal in A.
Offset → offset of the demanded signal in A.
Note, gains for current direct loops should be the same as gains for current quadrature loop
Current quadrature Tune window
If you want to get a deeper understanding of how this current quadrature loop is implemented inside the drive, please refer to the following documentation: Current modes (CSC, C, CA).
Parameters to tune
Kp → gain whose control action is proportional to the error between the current quadrature demand and actual values.
Ki → gain whose control action is proportional to the error between the current direct demand and actual values integrated over time.
Kr → gain that allows changing the architecture of the controller from an I+P (Kr = 0) controller to a PI (Kr = 1) controller. Intermediate values of Kr between 0 and 1 will provide a hybrid controller with both I+P and PI characteristics, weighted proportionally to the value of Kr.
Additional parameters
Current quadrature loop max. out → maximum voltage that will be applied to the phases of the motor. It acts as a saturator.
Current quadrature loop min. out → minimum (negative sign) voltage that will be applied to the phases of the motor. It acts as a saturator.
Max current → maximum current that will be applied to the phases of the motor.
Signal Generator
Gen. Signal → signal that with be generated with the settings below. For this workspace, this is the current quadrature set-point.
Signal → shape of the generated signal wave. At the moment this can only be a square wave.
Frequency → frequency of the generated signal in Hz.
Amplitude → amplitude of the demanded signal in A.
Offset → offset of the demanded signal in A.
Velocity Tune window
If you want to get a deeper understanding of how this velocity loop is implemented inside the drive, please refer to the following documentation: Velocity modes (CSV, PV, V).
Parameters to tune
Kp → gain whose control action is proportional to the error between the velocity demand and actual values.
Ki → gain whose control action is proportional to the error between the velocity demand and velocity actual values integrated over time.
Kd → gain whose control action is proportional to the derivative of the error between the velocity demand and velocity actual values in a given instant of time.
Additional parameters
Velocity loop max. out → maximum current that will be inputted to the current quadrature loop. It acts as a saturator.
Velocity loop min. out → minimum (negative sign) current that will be inputted to the current quadrature loop. It acts as a saturator.
Max velocity → maximum velocity that the motor will never be able to exceed.
Signal Generator
Gen. Signal → signal that with be generated with the settings below. For this workspace, this is the velocity set-point.
Signal → shape of the generated signal wave. At the moment this can only be a square wave.
Frequency → frequency of the generated signal in Hz.
Amplitude → amplitude of the demanded signal in rev/s.
Offset → offset of the demanded signal in rev/s.
Position Tune window
If you want to get a deeper understanding of how this position loop is implemented inside the drive, please refer to the following documentation: Position modes (CSP, PP, IP, P).
Parameters to tune
Kp → gain whose control action is proportional to the error between the position demand and actual values.
Ki → gain whose control action is proportional to the error between the position demand and position actual values integrated over time.
Kd → gain whose control action is proportional to the derivative of the error between the position demand and position actual values in a given instant of time.
Additional parameters
Position loop max. out → maximum velocity that will be inputted to the velocity loop. It acts as a saturator.
Position loop min. out → minimum (negative sign) velocity that will be inputted to the velocity loop. It acts as a saturator.
Max position → maximum absolute position that will not be exceeded while the motor is enabled. It acts as a limit.
Min position → minimum absolute position that will not be exceeded while the motor is enabled. It acts as a limit.
Signal Generator
Gen. Signal → signal that with be generated with the settings below. For this workspace, this is the position set-point.
Signal → shape of the generated signal wave. At the moment this can only be a square wave.
Frequency → frequency of the generated signal in Hz.
Amplitude → amplitude of the demanded signal in rev.
Offset → offset of the demanded signal in rev.
Position tracking error
If this is the first time that you try to move the motor in position mode (any type), you will most likely get a "Position tracking error" fault right after you do "Target latch" your first position set-point. Do not panic, this is completely normal. What is happening is that the drive is simply applying a protection based on the position following error window/timeout parameters. Since your initial PID tuning for position
In order to overcome this, you can do either one of the following:
Set the position following error option code register (key 0x0617) to 1 in order to overwrite this protection so that it does not apply anymore
Increase the position following error window/timeout values to larger values so that the tolerance interval is large enough to not trigger the fault
Set position following error timeout to 0
For more on the following error concept, please refer to the documentation: Position modes (CSP, PP, IP, P).
Always remember that if it makes your life easier you can add additional variables to your workspace in order to make the tuning better and save the workspace configuration to a file. More on this here: Workspaces | How-to-save/load-workspaces