Primary Absolute Slave 2
This step explains how to configure the secondary BiSS-C absolute encoder (daisy chain) properly in the configuration Wizard. In order to do it, you need to properly fill the parameters associated with this encoder in the Control widget (green square below). After this, you can validate that the position readings are correct both by taking a look at the values in the Display widget (blue square below) and performing the absolute encoder test (orange square below) in order to make sure that the encoder readings and pole pairs settings of the motor are correct.
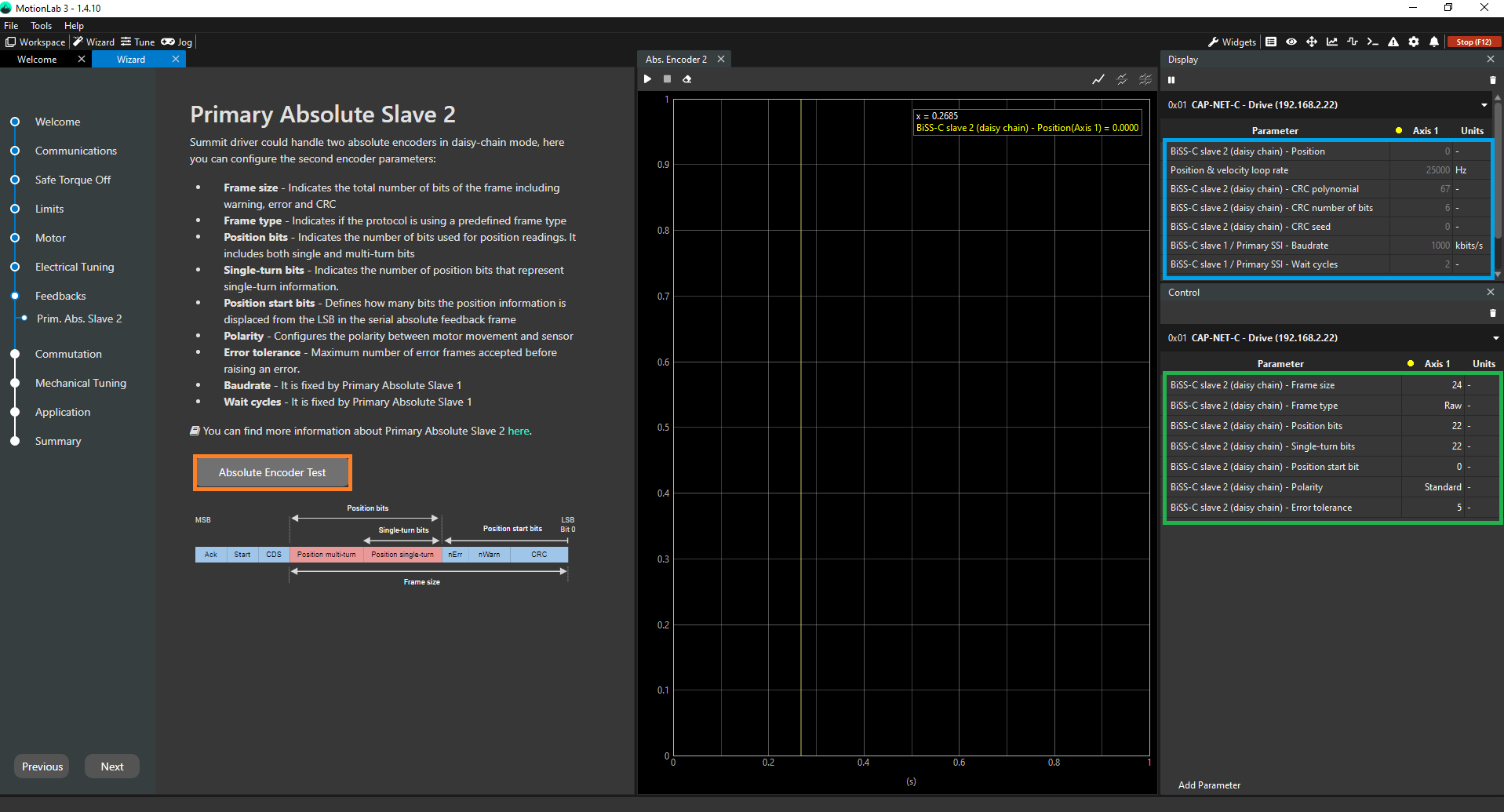
Parameters to configure
Frame size → Indicates the total number of bits of the frame. These include position bits, special bits, warning, error and CRC bits, etc.
Start, CDS and ACK bits do not need to be included in this frame size.
Frame type → Indicates the format of the received frame. This parameter allows parsing frames in a specific way. For example, the BiSS-C BP3 profile frame type will assume there are CRC, error and warning bits and will use them to detect errors in the frame. For unsupported frame types, use raw or raw gray modes. These modes allow to read the position from any frame type without processing special bits such as CRC or error flags.
Position bits → Indicates the total number of bits used for position readings. This includes single-turn and multi-turn position bits.
Single-turn bits → Indicates the number of bits that represent single-turn position data.
Position start bit → Defines how many bits the position information is displaced from the LSB in the serial absolute feedback frame.
Polarity → the polarity of the feedback sensor is a parameter that relates how the position readings change when a positive voltage is applied to the phases of the motor. It can either be "Standard" or "Reversed".
Understanding how the polarity works
If with polarity set as "Standard, the position increases when a positive voltage is applied, then the polarity is correct as "Standard". On the other hand, if the position readings were to decrease, then the polarity setting would be wrong and you would need to change it to "Reversed" for this particular feedback sensor. Having a correct polarity setting is essential to having the sensor working properly and this is exactly what the absolute encoder test is meant to determine. On an additional note, the polarity of the digital halls does not relate to the polarity of any other feedback sensor in the system (they can be the same or opposite, it does not matter).
Limitations of total frame size and total position data
Just like with the primary absolute encoder and the secondary SSI encoder, the secondary BiSS-C encoder has certain size limitations for the maximum number of bits of the total BiSS-C frame and the total number of position bits that can be part of that frame. The restrictions are the following:
Maximum frame size → 32 bits
Maximum position data → 24 bits (32 bits - 6 CRC bits - 2 error/status bits)
This means that any encoder with a frame larger than 32 bits will not be read correctly from the drive (even if the position data bits are < 24 bits). In addition to this, there are additional limitations that are applied taking into account the frame size and position bits of the primary BiSS-C encoder:
BiSS-C slave 1 frame size + BiSS-C slave 2 frame size <= 64 bits
BiSS-C slave 1 positions bits + BiSS-C slave 2 position bits <= 48 bits
Configuration examples
If you want to check some configuration examples of absolute encoders, please refer to the Primary Absolute Slave 1 section.
Absolute encoder test
This test has the following purposes:
Validate that the absolute encoder parameters and pole pair parameters introduced by the user are correct → this is done by moving a certain predefined range of motion and counting the position readings so if they match with the expected ones then the test turns successful. If they do not match, then you get a failure and you need to recheck both parameters to see which one could be wrong.
Determine the polarity of the absolute encoder → this is done by applying always positive voltage first and then negative voltage and seeing how the position readings change. Please note that this polarity determination is not done if the previous validation does not turn out successfully.
Therefore, this test has only two possible outcomes:
Failed test
Success test
Absolute encoder quick verification
If you get a failure in this test, a quick check that you can do is verify the resolution of the encoder by moving the shaft manually one full revolution (motor is disabled) and checking that the position readings (blue square in the initial picture) change in an increment equal to 2^number of single-turn bits. This will validate the single-turn, the position starting bit, the frame size and type parameters. In a system with a gearbox, this can be trickier but you could move the motor in voltage mode (using the Jogs) and check that a full revolution on the output equals an increment in position readings equal to (2^number of single-turn bits) * gear ratio of the gearbox.